
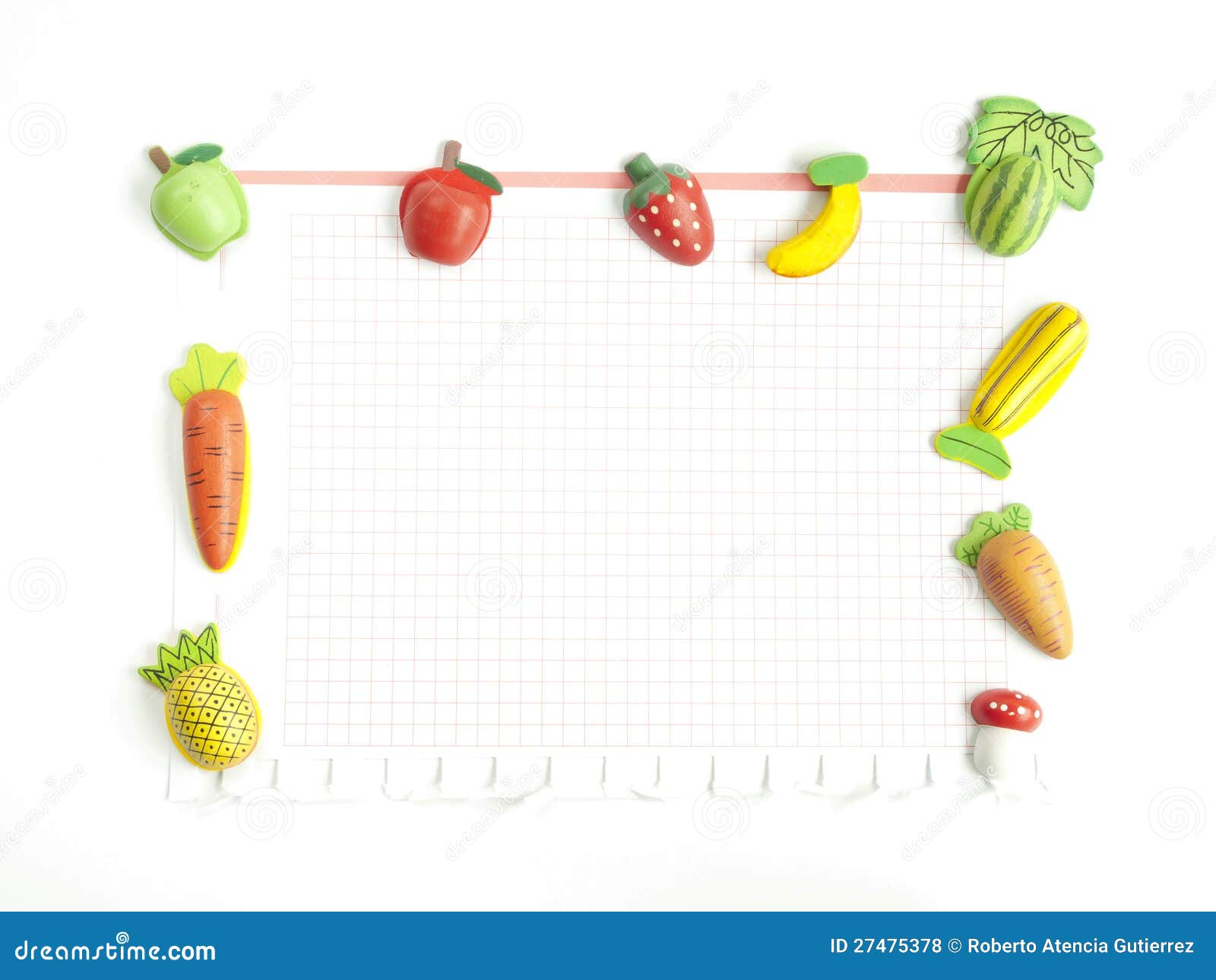
BAAM printed NdFeB polyphenylene sulphide bonded magnets. Furthermore, recovering rare earth elements from waste scraps is not an easy task, especially considering the rapid oxidation of such elements. Conventional manufacturing methods for permanent magnet production are considered inefficient, as they can generate a sizeable waste when magnets are shaped to the required shapes and sizes through cutting and slicing. Rare earth magnets might be the strongest permanent magnets, but they rely on the availability of rare earth elements, and this supply is currently in crisis, leading to high costs of raw materials. “3D printing bonded permanent magnets could reduce the use of scarce rare earth elements, reduce energy and labour requirements, and explore endless capabilities of magnet shapes. Some of the critical properties of magnets for certain applications are corrosion resistance, mechanical strength, thermal stability, ability to be shaped on request, coercive force, and of course, cost. Rare earth magnets are the strongest among permanent magnets, consisting of alloys containing rare earth elements, such as Neodymium (Nd), and Dysprosium (Dy). Each type has distinct advantages and disadvantages, which affect the popularity for different applications. There are several types of permanent magnets, such as rare earth magnets, samarium cobalt magnets, alnico magnets (based on an alloy of Aluminium, Nickel, and Cobalt), ceramic magnets, magnets produced via injection moulding, and magnets of flexible structure. Their difference arises from their magnetism (magnetic ability), which can be temporarily induced upon exposure near a magnetic field (soft magnets), permanent and unaffected due to constantly aligned atomic structure or caused by electricity passing through a coil (electromagnets). There are three main categories of magnets, namely soft (temporary), permanent, and electromagnets. From decorative fridge magnets and door closing systems, to magnets used in electronics, motors and generators, magnets have a very large market, which has been expanding with the development of environmentally friendlier technologies. His work shows that additive manufacturing can be used successfully for bonded permanent magnet fabrication, leading to products with high thermal stability and corrosion resistance.Īll of us have made use of magnets at one time or another. To reduce waste and labour associated with permanent magnet fabrication, Dr Mariappan Parans Paranthaman, a corporate fellow at Oak Ridge National Laboratory, developed a bonded magnet fabrication method using additive manufacturing, also known as 3D printing. Permanent magnet production, however, relies on the use of critical rare earth elements, which are scarce. Permanent magnets are used in numerous everyday and industrial applications, for example door locks and motors and generators.
